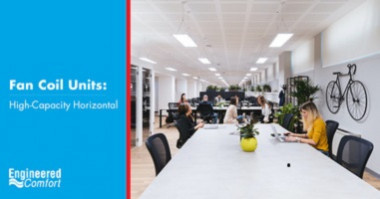
While the in-room horizontal fan coils units may be the highest volume product used in the industry due to the numbers used in hospitality, the high-capacity horizontal fan coil units are the most versatile. The span of sizes, options, and variants make these units suited for residential, office, & industrial applications. High-capacity refers to the larger sizes up to 4,000 CFM and the ability of the fans to handle 3/4" w.g. of static pressure. Both allow for more complex ductwork and air distribution than other designs. Learning how each of the components in the construction works together to deliver comfort will help select the best product for your application.
5 Consideration Variables
The previous article highlighted the five variables to consider when selecting a horizontal fan coil unit. The variables are capacity, static pressure, available ceiling space, sound sensitivity, and outside air capabilities. The high-capacity fan coil units perform per the information below:
- Capacity Requirements
- 400-4,000 CFM
- 1-14 Tons Cooling
- 20-200 MBH Hot Water Heating
- 1-16 KW Electric Heating
- External Static Pressure
- High, up to 0.75" w.g.
- Pressure independent motors available
- Available Ceiling Space
- Sizes 4-24, 17"
- Sizes 30-40, 23"
- Sound Sensitivity
- Low
Though these units are a little taller, 17-23", if the application has enough ceiling space, there are units that will meet the needs of any project. With modulating EC motors these units will cover from 200 CFM to 4,000 CFM.
Construction
As the name suggests, the two main parts of a fan coil are the fan and the coil.
Fans
There are three fan motor technologies available for these units:
- 3-Speed PSC
- 3-Speed ECM
- Modulating ECM
A 3-Speed PSC uses two circuits, one of which has a capacitor that creates a current lag between the windings to generate the torque to start the motor. The capacitor generates heat and therefore reduces the efficiency of the motor. A 3-speed design has three different motor winding lengths to control the speed. The shortest winding delivers the highest speed, the longer winding is medium, and the longest is the slowest speed. By using longer windings, or higher resistance, to reduce the speed the motor becomes less efficient at slower speeds. A PSC motor is around 50% efficient and the pre-set speeds cannot respond to changes in static pressure in the system.
ECM, or Electronically Commutated Motors, utilizes a processor to commutate the AC power to perform like DC Power.
Commutation - the regulation or reversal of an alternating current.
The processor controls how the power is delivered to the motor to induce motor torque. With the higher amount of control, comes higher motor efficiencies. Also, the ECM motors are brushless, which means there is no physical connection between the rotor and stator that would induce inefficiency into the system. The electronic control of the motor enables slowing or speeding the motor to a specific speed within its speed range. A 3-speed motor has a program with pre-set speeds. The modulating ECM has a controller that can respond with any speed based on the control system. The modulating motors enable advanced control systems that deliver the right amount of conditioning for any requirement in the room.
Coils
The coil transfers heat to/from the air to provide conditioning to the space. There are three types of coils used in hydronic fan coils:
- Hydronic
- Chilled Water
- Hot Water
- Electric Heating Coils
A note on Coil Location: Blow-through vs. Draw-through
One differentiator for Nailor High-Capacity Fan Coil units is the location of the hydronic coils. Nailor 35 and 37FH models have a draw-through configuration, with many benefits over the industry-standard blow-through design.
- Blow-through designs have a blast area, where a disproportionate amount of air flows through a small area on the coil face. Drawing the air ensures the entire coil face contacts the air during the process increasing the thermal efficiency of the coil.
- A blast area can cause high coil air velocities, potentially carrying condensation into the downstream ductwork.
- Draw-through design enables smaller outlet duct sizes because they are sized based on the fan outlet instead of the coil.
The result is a more thermally and energy-efficient unit requiring lower-cost supply ductwork to the space.
Hydronic Coils
Chilled Water
Cooling coils use chilled water, typically 45°F, to remove heat from the air in the space. They're made of a coil of piping connected by a series of fins, that increase the surface area the air encounters to increase heat transfer. The heat transfer through a coil is affected by water temperature, flow rate, and coil size and circuiting. Colder water pulls more heat from the air than warmer, though it is more expensive to create and maintain in the system. The design standard 75° indoor dry-bulb temperature has a wet-bulb temperature of 55° at 50% humidity and 45° EWT achieves a 55° leaving air temperature required to provide dehumidification. As water flow rates through the coil increase so does the heat transfer, but higher rates require pump higher pressures, and the benefits could outweigh the costs associated with higher rates. Coil size: length, width, and depth also affect heat transfer. Coil depth is measured in rows, ranging from 1-6 rows. Coils with more rows increase the time the air is in contact with the coil, increasing heat transfer. Deeper coils also aid in latent loads, giving the moisture in the air longer to condense onto the coil.
Another differentiator for the Nailor 35 and 37FH units is the cooling coil has a fully encased and insulated cooling coil.
Hot Water
Hot water coils perform in the same manner as chilled water. They typically have higher ∆T water with the room air and therefore can be smaller than chilled water coils. The default location for these coils is in the reheat position. This allows for dehumidification cycles where the cooling coil pulls moisture from the air and the heating coil reheats it to maintain comfort in the space.
Electric Coils
Electric coils utilize electric resistance wires to heat up and warm the air. They are sized based on KW. To eliminate the chance of overheating they must have a minimum airflow of 70 CFM per KW. The electric coil is on the fan discharge of the high-capacity horizontal fan coil units.
Accessories
The accessories for the high capacity units are the same as the In-room units:
- Valve Packages
- Control Valve
- Auto Flow Control
- Shut-off valves
- Accessories
- Y
- Unions
- PT Ports
- Factory Installed Controls
- Matching Access Panels/Return Grilles
- Condensate Pumps
- Outside Air Inlets
I want to highlight a few differences enabled by the higher capacity and better fans on with these units vs. the in-room designs. The ability to pair a modulating valve with a modulating fan allows the unit to meet the specific needs of the space. The fan speed is controlled by the thermostat in the space and the valve setting is controlled by the leaving air temperature. The unit finds the exact amount of cooling/heating and maintains comfort at the right fan speed and valve setting. This increases the efficiency and reduces sound from the unit.
The Nailor 35 and 37FH have an innovative option for the outside air inlet. The draw-through design allows the outside air to be introduced downstream of the coil. Pairing this design with a Dedicated Outside Air System (DOAS) allows you to use fan coils in the areas where the latent load cannot be met with sensible cooling coils.
Selections
Using a manufacturer's selection software will aid in the decisions for which product is right for your project. Nailor has software for its products, called SelectWorks, that allows you to enter the required capacities, airflows, and design conditions, and the software will show you the options that meet the needs of the project. If you are working on a project and need help with what type to design around or selections, don't hesitate to reach out to us.